How to avoid the cracks of Tungsten tips in Resistance Spot Welding?
Resistance spot welding is a crucial process in manufacturing, particularly in automotive production. Tungsten electrode tips play a vital role in this process, but they are susceptible to cracking under certain conditions.
Causes: Tungsten electrode tip cracks can result from thermal and mechanical stress, impurities in the material, and rapid heating and cooling cycles.
Strategies to Prevent Cracks:
- Proper electrode selection: Choose high-quality tungsten electrodes and consider shape and size.
- Optimize welding parameters: Adjust current, voltage, and welding speed, and use pulse welding techniques.
- Preheat the workpiece: This reduces thermal shock on the electrode tip.
- Shield the welding environment: Minimize oxidation by using inert gas shielding.
- Ensure cleanliness: Thoroughly clean the workpiece and electrode tip to prevent contamination.
Outline
Introduction
A. What is resistance spot welding?

Resistance spot welding is a widely used welding process in manufacturing, particularly in the automotive industry. It involves the joining of two or more metal sheets by applying pressure and electrical current to localized areas, creating a series of weld spots.
B. Why are tungsten tips important?
Tungsten electrode tips are essential components in resistance spot welding machines. They serve as the point of contact where the electrical current is applied to the workpieces, generating heat to melt and fuse the metals together. The quality and condition of the tungsten electrode tips directly impact the effectiveness and reliability of the welding process.
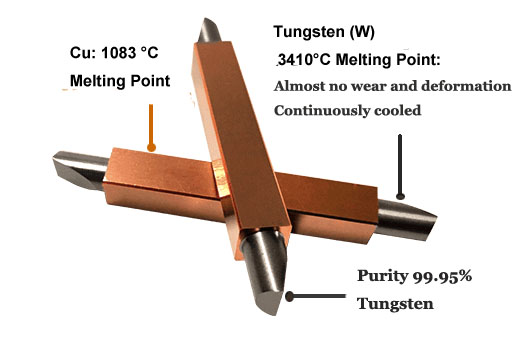
C. The problem: electrode's tungsten welding tip cracking
Despite their importance, tungsten electrode tips are likely to crack under certain conditions. This issue can arise due to various factors such as thermal stress, mechanical stress, impurities in the tungsten material, and rapid heating and cooling cycles.
Cracks in the electrode tips can lead to reduced weld quality, decreased productivity, and increased downtime, making it crucial to address and prevent this issue proactively!
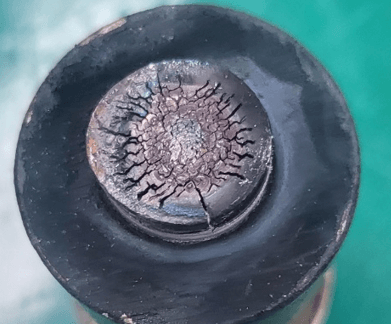
II. The Causes of Tungsten Electrode Tip Cracks
Cracks in tungsten electrode tips during resistance spot welding can be attributed to various factors, including
- Welding heat
- mechanical stress
- Impurities of Tungsten
- Rapid heating and cooling cycles
Understanding these causes is essential for implementing effective strategies to prevent electrode tip cracking and ensure the longevity and reliability of the welding process.
A. Thermal stress during welding
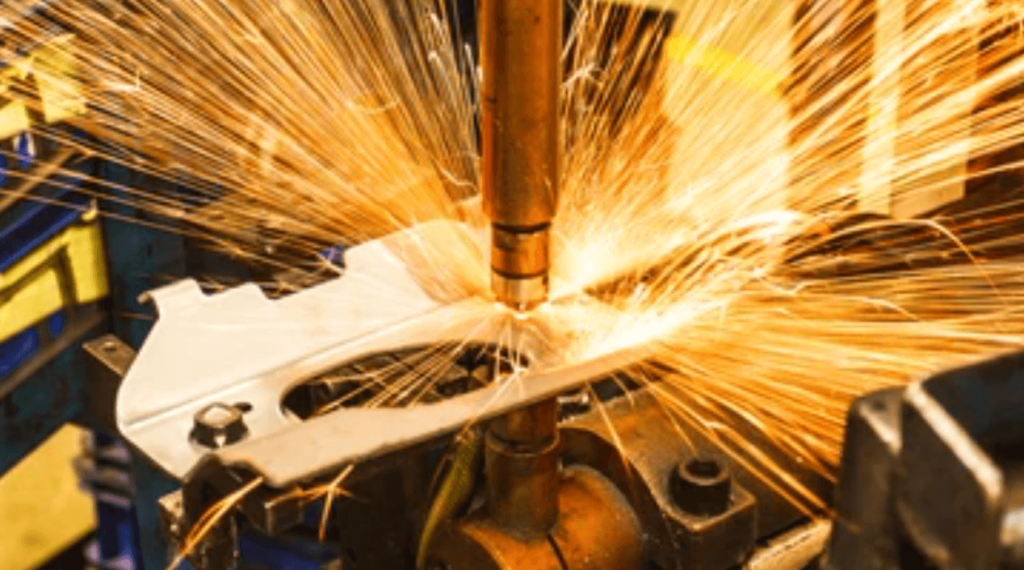
When electricity passes through the tungsten electrode tip during welding, it generates intense heat, causing rapid expansion and contraction of the material. This thermal cycling can create significant stress within the electrode tip, especially if the heat is not distributed evenly. The resulting thermal stress may exceed the material’s tolerance, leading to cracks in the electrode tip.
B. Mechanical stress from electrode movement
During resistance spot welding, the tungsten electrode tip may experience mechanical stress from repeated movements, such as contact with the workpiece or retraction after welding. These mechanical forces can weaken the material over time, making it more susceptible to cracking, especially if the electrode tip is not properly maintained or aligned.
C. Impurities in the tungsten material

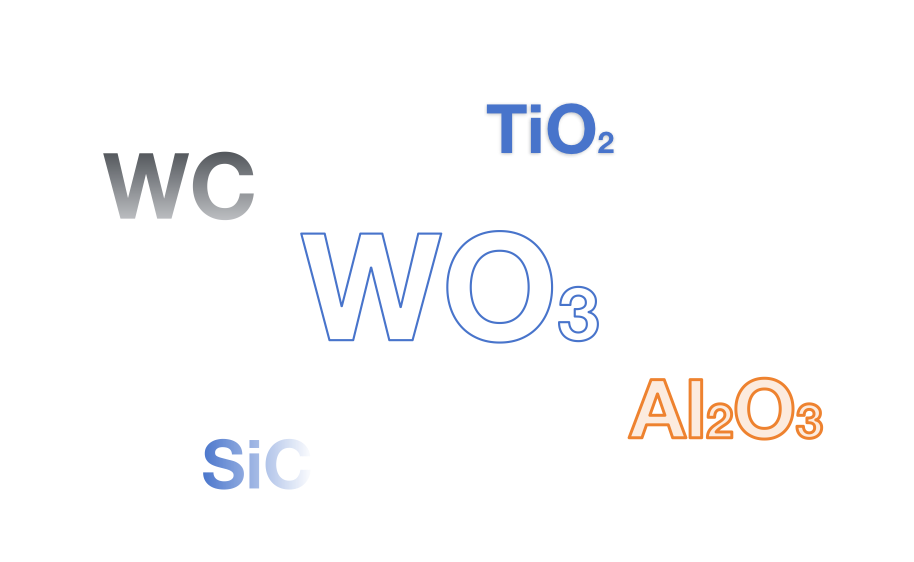
Impurities or defects in the tungsten material used to manufacture electrode tips can create weak points that are prone to cracking under stress.
Common impurities include oxides, carbides, such as WO3, TiO2, WC, SiC and other foreign particles that may be introduced during the manufacturing process. These impurities can compromise the structural integrity of the electrode tip, making it more susceptible to failure.
D. Rapid heating and cooling cycles
The rapid heating and cooling cycles experienced by tungsten electrode tips during resistance spot welding can also contribute to cracking. As the electrode tip heats up during welding and then rapidly cools down after each weld, it undergoes thermal expansion and contraction, which can create internal stresses within the material.
Over time, these repeated cycles of heating and cooling can weaken the electrode tip and lead to the formation of cracks.
III. Prevent Tungsten Weld Tip Cracks
A. Proper electrode selection
Choosing high-quality tungsten electrodes: Selecting tungsten electrodes from reputable manufacturers ensures superior quality and consistency in material composition. Such as the purity above 99.95%, the uniform internal structure and compactness.
High-quality electrodes are less likely to contain impurities or defects that can contribute to tip cracking.
Tungsten Raw Materaisl


Yolo’s uniform particle

Some factory’s uniform particle
B. Optimizing welding parameters
- Adjusting current, voltage, and welding speed:
Fine-tuning welding parameters such as current, voltage, and welding speed helps control heat input and distribution, reducing thermal stress on the electrode tip.
Experiment with different parameter settings to find the optimal combination that minimizes tip cracking while ensuring satisfactory weld quality.
- Implementing pulse welding techniques:
Pulse welding involves alternating between high and low current levels during the welding process, allowing for more controlled heat input and reduced thermal stress on the electrode tip. Pulse welding techniques can help prevent overheating and cracking in tungsten electrode tips, especially when welding thin or heat-sensitive materials.

C. Preheating the workpiece before welding
Preheating the workpiece before welding helps reduce thermal shock on the tungsten electrode tip by promoting more gradual heating and cooling cycles. This minimizes the risk of thermal stress-induced cracking in the electrode tip. Use preheating techniques such as induction heating or resistance heating to achieve the desired temperature range for the specific material being welded.
D.Shielding the welding environment to minimize oxidation
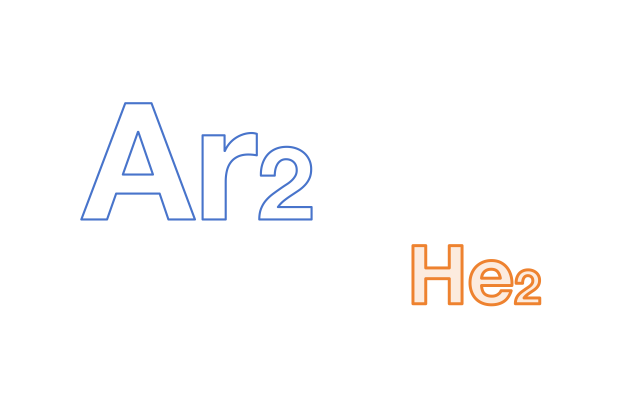
Protecting the welding environment with inert gas shielding, such as argon or helium, helps minimize oxidation of the tungsten electrode tip during welding. Oxidation can weaken the electrode material and make it more susceptible to cracking. Use gas lenses, trailing shields, or gas curtains to maintain a consistent shielding atmosphere around the weld zone and electrode tip.
E. Cleanliness of the workpiece and electrode
Thoroughly clean the workpiece and tungsten electrode tip before welding to remove any contaminants that could compromise weld quality or contribute to tip cracking. Use solvents, wire brushes, or dedicated cleaning solutions to remove dirt, oil, rust, or other debris from the surfaces. Proper cleanliness helps ensure good electrical contact between the electrode tip and workpiece, minimizing resistance and heat generation during welding.
Our story
About YOLO
As a tungsten and molybdenum products factory, we prioritize quality and efficiency, allowing us to offer competitive factory prices without compromising on the excellence of our products. Whether you’re a small workshop or a large manufacturing facility, we’re committed to providing you with the customized spot welding electrodes you need to achieve outstanding welding results.
Contact us today to discuss your spot welding requirements and discover how our customized electrodes can enhance your welding processes at a competitive factory price.

Spot Resistance Welding Electrode
Get Factory Price Start From Custom Size in China
As an expert manufacturer, Yolo offering high quality custom Spot resistance welder tips solution to evaluate your project!